|
Moldmaking is one of the services that I offer. This particular type of mold is designed to support the "low volume production" of a commercial product. Consequently, it's a bit different than provisional molds for fine art that I describe in other articles.
Usually, a mold like this will produce about 50 resin parts before it starts to have problems that may require repairs (or as we like to say, "retooling"). Resin is chemically tough on silicone rubber and essentially ages the rubber. "50 pulls" is what the manufacturer of the rubber will tell you. Fortunately, there are a number of ways to greatly extend the useful life of the rubber and the client probably knows them all. I suspect they will pull far more than 50 parts from the low volume production mold show below.
|

Low Volume Production Mold ready to receive resin.
|
Low Volume Production Mold Design Requirements:
* Sufficient space on the mother mold to use clamps instead of bolts * Very fast dissassembly * Fast divestment of the cast part without twisting and straining of the rubber * Thick enough rubber for "dimensional stability" to support fast reassembly of the mold without the use of "rubber to mother-mold" keys * "Rubber-to-rubber" keys that do not slow the process of mold reassembly * Robust construction without excessive weight * Suitable venting and funnels for pouring their type of expanding foam resin. * Top and bottom pieces that support the accurate placement of an internal part prior to casting * A top piece with a large enough rubber area to support the easy clean-up of foam resin overflow * A mother mold so constructed as to make the top piece level when used on a level bench * Quick-release, rubber "stoppers" that fit the three lower pour spouts
|
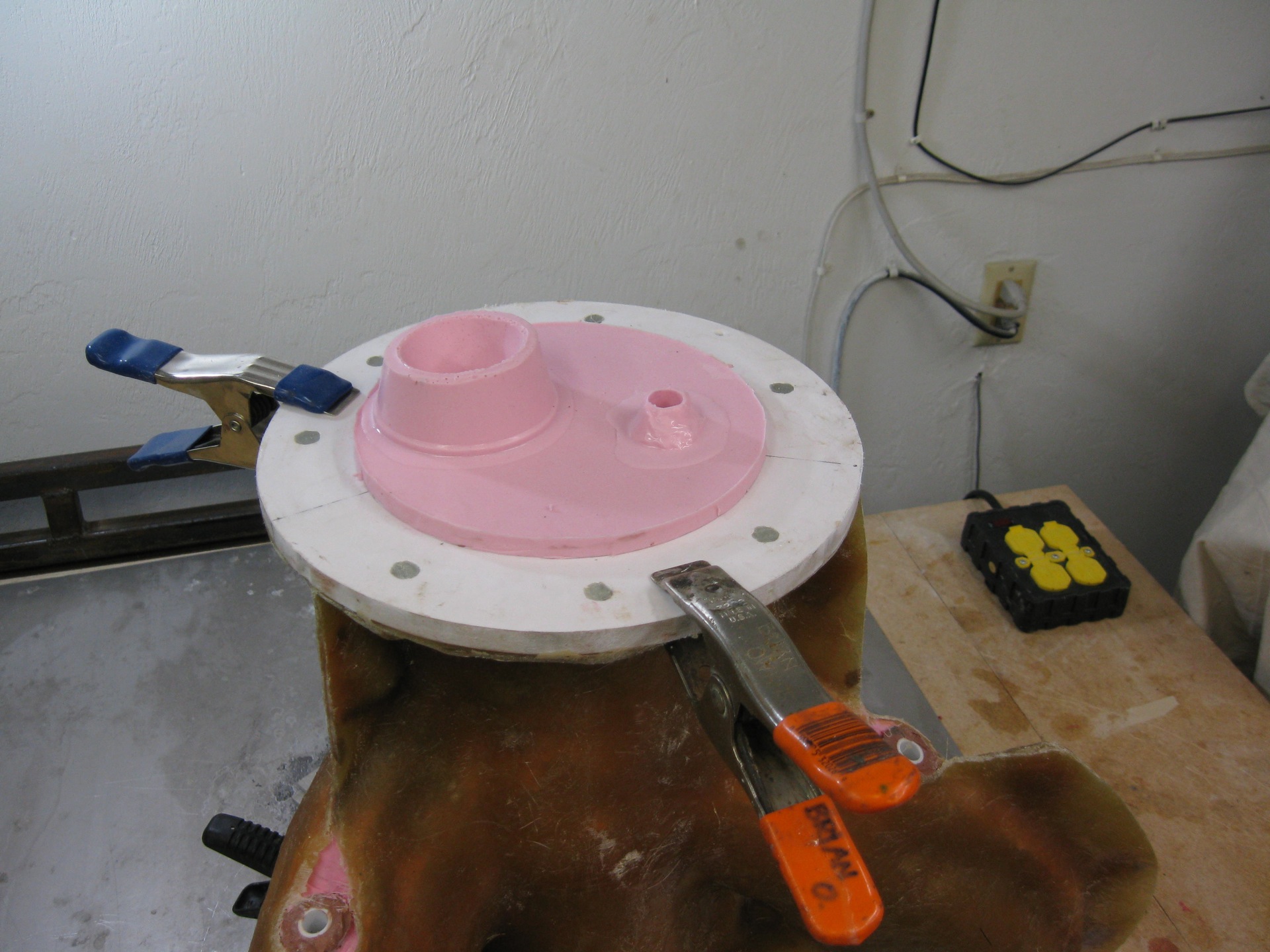
Top of the Low Volume Production Mold with pour spout and vent.
|
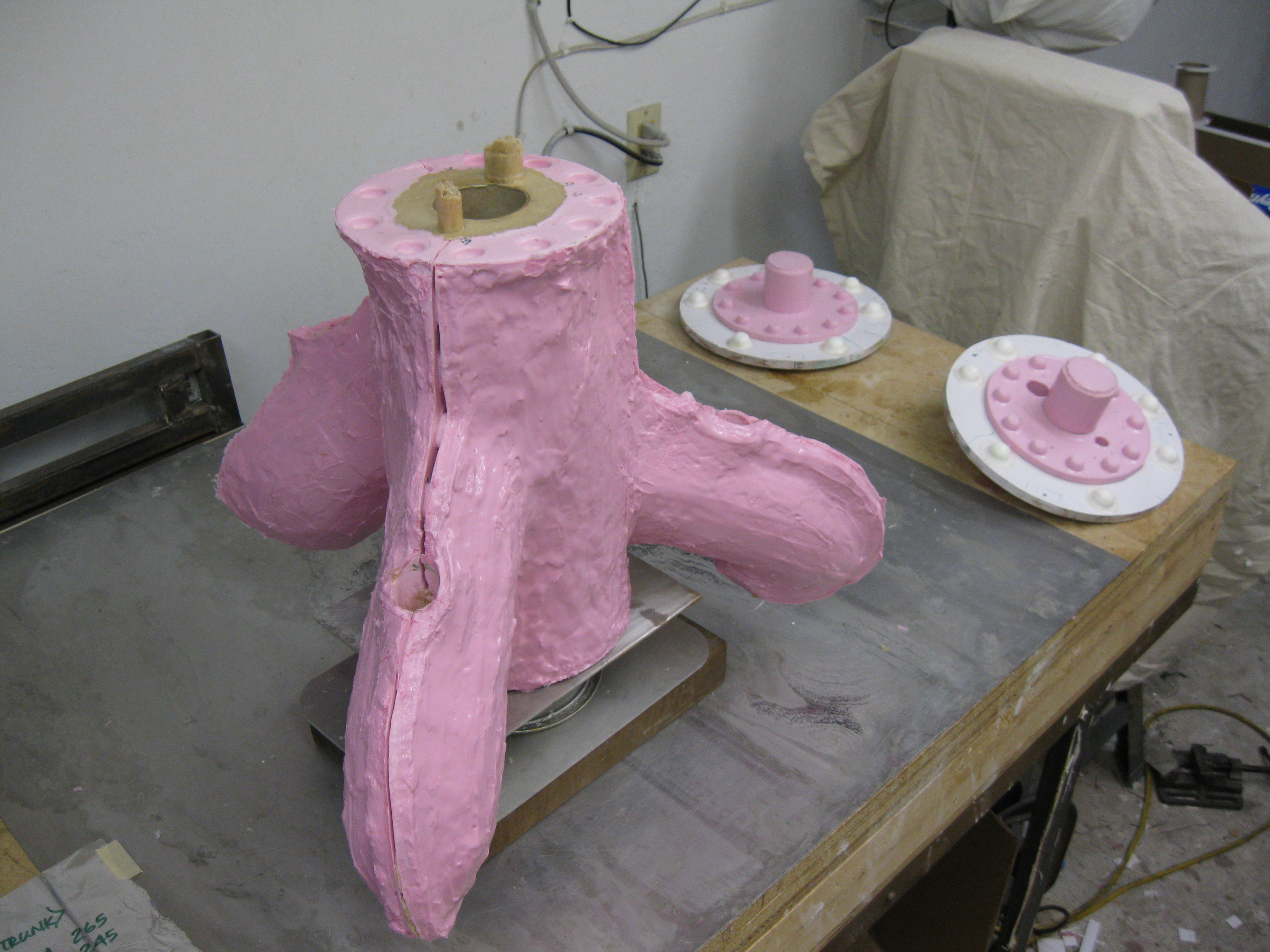
The mother mold has been removed in order to divest the cast resin part. The top and bottom pieces are designed to support the accurate placement of an internal part prior to casting.
|
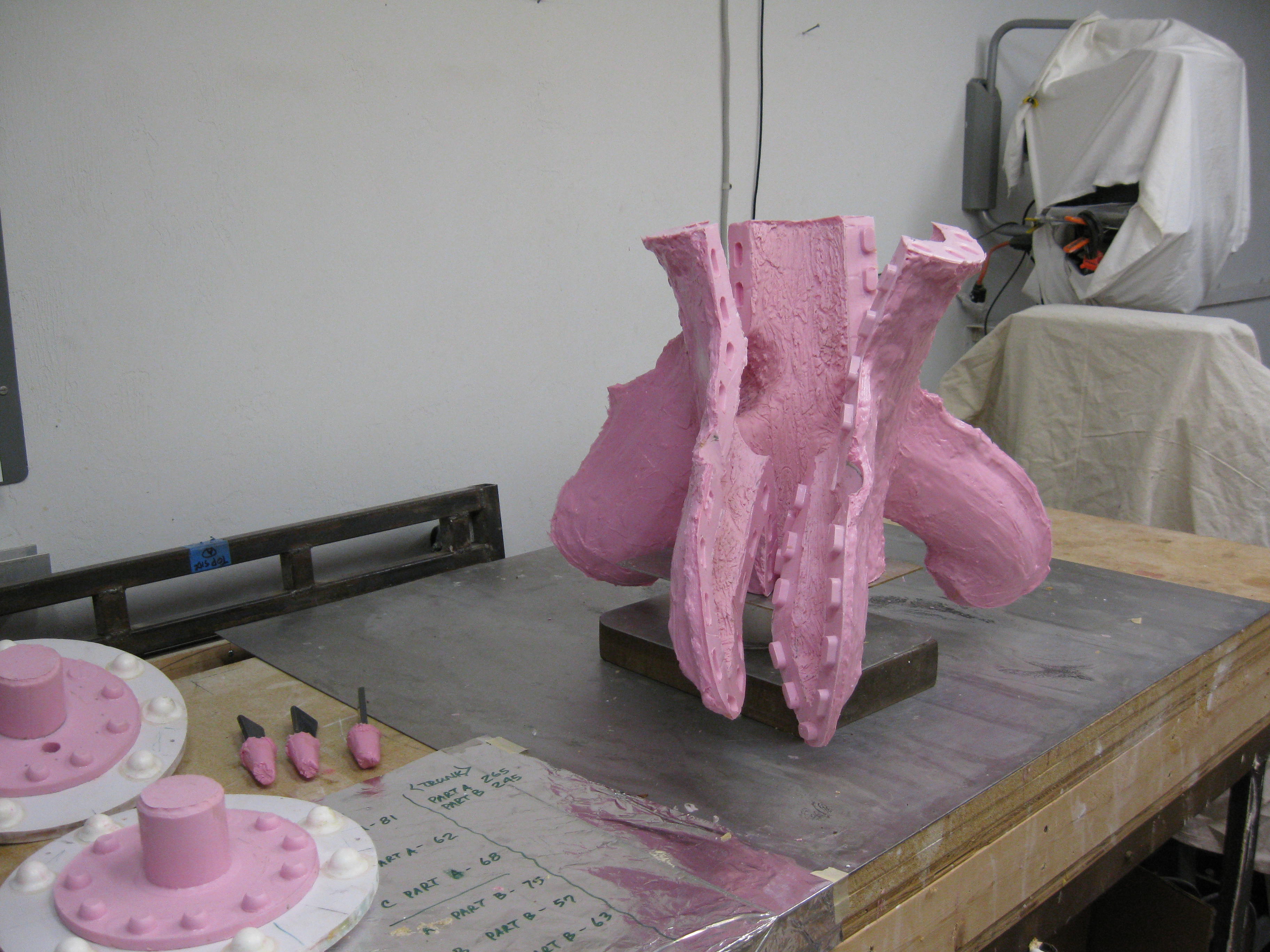
With the cast resin part removed, the rubber holds its shape for easy reassembly.
|
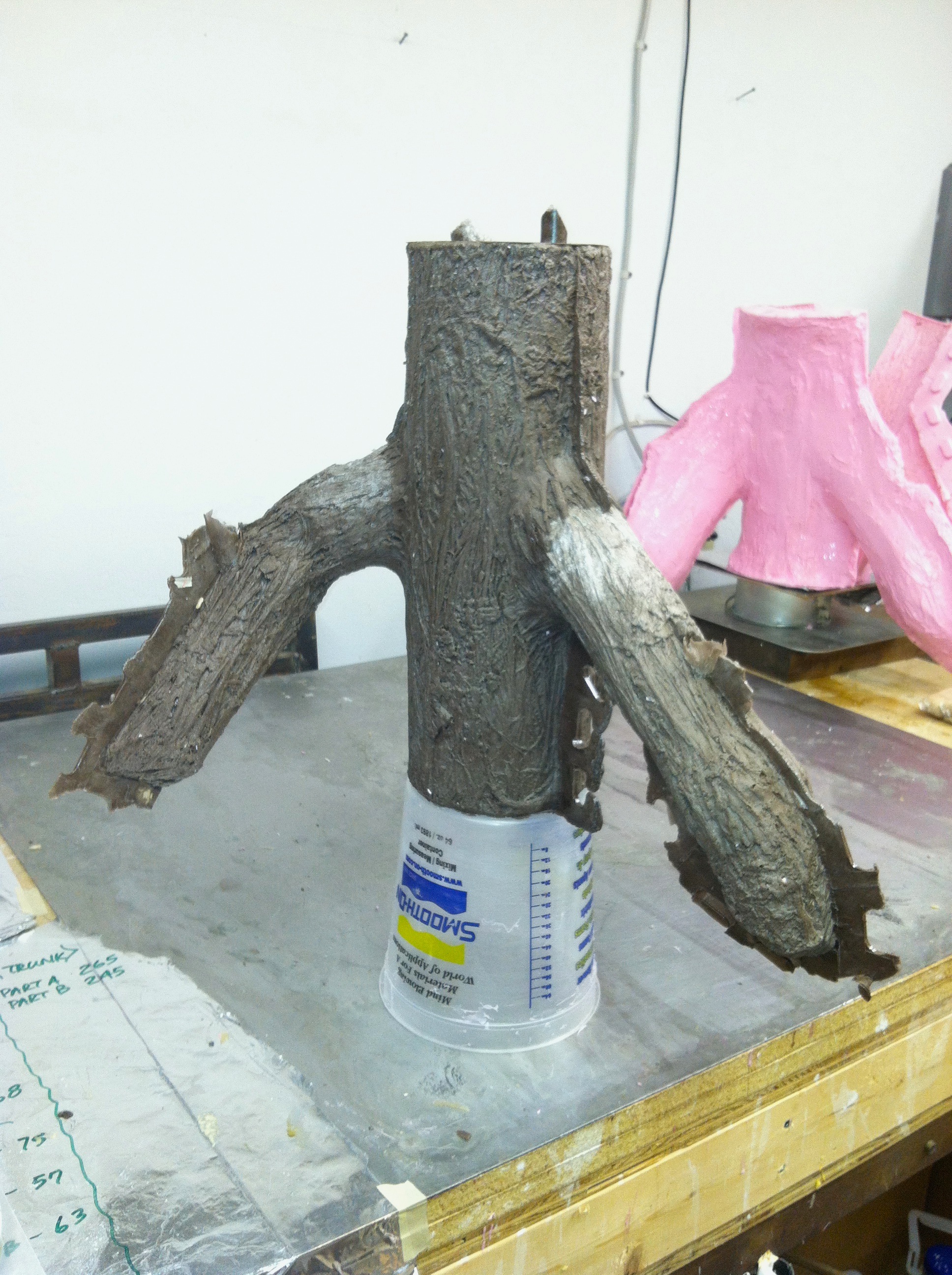
The cast resin part pulls up out of the rubber with ease. The resin is actually expanding foam that creates pressure within the mold reslting in the flashing you see above. This trims off easily.
|
Follow-up Thoughts
This low volume production mold will suit the client just fine for now. I imagine that it will be replaced with another type of mold as the need for production increases.
This mold was the first time I considered using new methods and materials. Usually, molds are a variation on the same theme using silicone rubber and fberglass reinforced plastic. The use of pvc for the top and bottom pieces was new for me. It's flat, cleans-up more easily than fiberglass and allowed me to work within my budget. The ultimate solution would have been to machine the top part out of solid teflon.
With a larger budget, I might have explored the use of a built-in, quick-release latch system as an alternative to spring clamps.
|